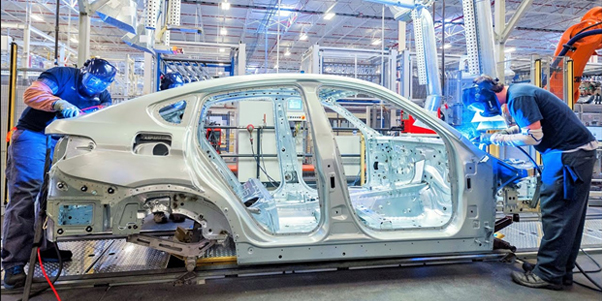
Several uses are there of the MIG welding. It is mainly used to repair recreational vehicles, cars, motorbikes, SUVs and vans. The main thing to note about the MIG welding is that it provides strong weld. Even for thin layered metals it provides a very strong weld. And, due to this fact it makes the MIG welding ideal for repairing any car parts from the exterior and the interior and, also assembling the car body parts. If you want that your vehicles should have years of use, then you should use MIG welding.
For welding particular types of sheet metal, wire mesh, or welded wire mesh, the spot welding is used. You can easily identify spot welding on many sheet metal goods, such as metal buckets etc. Aluminum alloys can be spot welded too. But it will require higher welding currents because of the thermal conductivity and electrical conductivity. In the automobile manufacturing industry there are common uses of spot welding To form a car sheet metal is spot welded universally. Spot welders can be completely automated.
What are the benefits of MIG welding and Spot welding?
In the spot welding, the base metal is not affected by the heat or does not undergo the large heat affected area. One of the best things that, you will know about spot-welding is that it is very easy and has high rate of production. It can applied to different metals to join them and it is a low-cost process.
Some of the benefits of MIG welding are that there is higher productivity, It is easy to learn and can produce great welds, the welding speed is fast and it offers clean welding, and it is versatile.
Where is the MIG welding Technique Used?
The methods of joining a material using heat are called MIG welding and Spot Welding. In both, MIG welding and Spot Welding, heat is used from electricity. Each process of MIG welding and Spot Welding has its own uses and benefits. The full form of MIG means a metal inert gas in which an electric arc is used to make the weld area, but there is no movement of the welding gas through the electrode holder i.e. of wire. The metal filler is fed from a different source, which has a larger/wider diameter than the wire of the electrode. So, this allows the MIG welding machine to use welding for thicker wires.
This MIG welding process is a bit different from the TIG welding and traditional arc welding, and one of the reasons for the same is that it does not get melted during the welding. The filler metal and the base metal is heated together, but they do not melt. Instead of that, a small area of both the metals is melted and then it is pressed together. So, this makes a weld which is which is strong and also has a smooth finish.
Where is the MIG welding Technique Used?
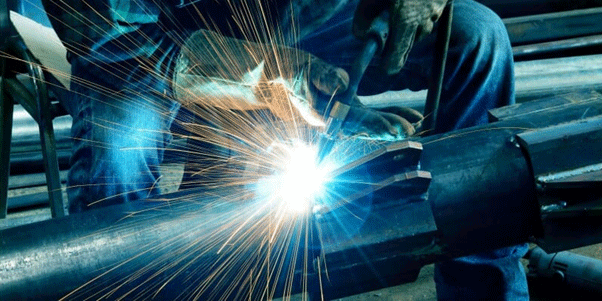
MIG welding is mainly used to weld copper alloys, magnesium, and aluminum. The MIG welding can also be used on steel, but the welds are not that strong as it is created or made by other methods. Mass productions are there that uses MIG welding machines, because they can be easily operated and it makes a consistent welds.
In Spot welding, two electrodes are used to create a weld. On the material to be welded, the electrodes are placed opposite each other. And, an electric current is passed through them. This makes a electric arc which heats up the material and when two pieces of metal is pressed together, the weld is created. Thin pieces of metals are welded together in spot welding. Compared to MIG welding, this type of welding is more fast and efficient way and does not require much equipment. Materials that are of similar thickness, it can be used only in those materials.
Suppose if the material is too thick, then the electrodes will not be able to create a weld, because there is too much of heat in the electrodes. Spot welding is used in different industries like that of packaging, automotive and construction.
Difference between – MIG and Spot Welding –
There are some key differences between the two. Let’s look at it – Wire and Electrode – When you are using a MIG weld you will have to continuously put a wire into a welding gun. You can bring these wires in a different range of diameter, depending on the project in which you are working. Whereas, spot welding is concerned, in spot welding electrodes is used to create the weld, and the electrodes are most of the time thicker than the wire, which means it can create a strong weld.
Pulse and Constant Current - In MIG welding, pulse current is used, which is used for a shorter time after which the machine stops the flow of electricity. So, if you have to weld another section, you will have to apply the current. But, in spot welding, there is a use of constant current. The current will move continuously through the electrode, while you are holding it in place against the material, which needs to be welded.
AC and DC Current – In MIG welding, either AC current i.e. alternating current is used or Direct current DC is used. But in spot welding, the case is different and spot welding uses direct current.
Welding Gas – To protect the weld from being contaminated, the MIG welding uses a cover or shielding gas and the most common type of gas that is used is argan and carbon di oxide, helium can also be used in addition. And, in spot welding there is no use of any type of gas.
Filler Metal – Filler metal is being fed into the weld, which is used in MIG welding (a separate piece of filler metal). The electric arc is used to melt the filler which joins the base metal to make the weld. In spot welding, the filler metal is the material that is used as a filler metal. In this 2 pieces of metal are taken up heated and pressed together to make the weld.